Understanding the World of China Mold: A Comprehensive Insight
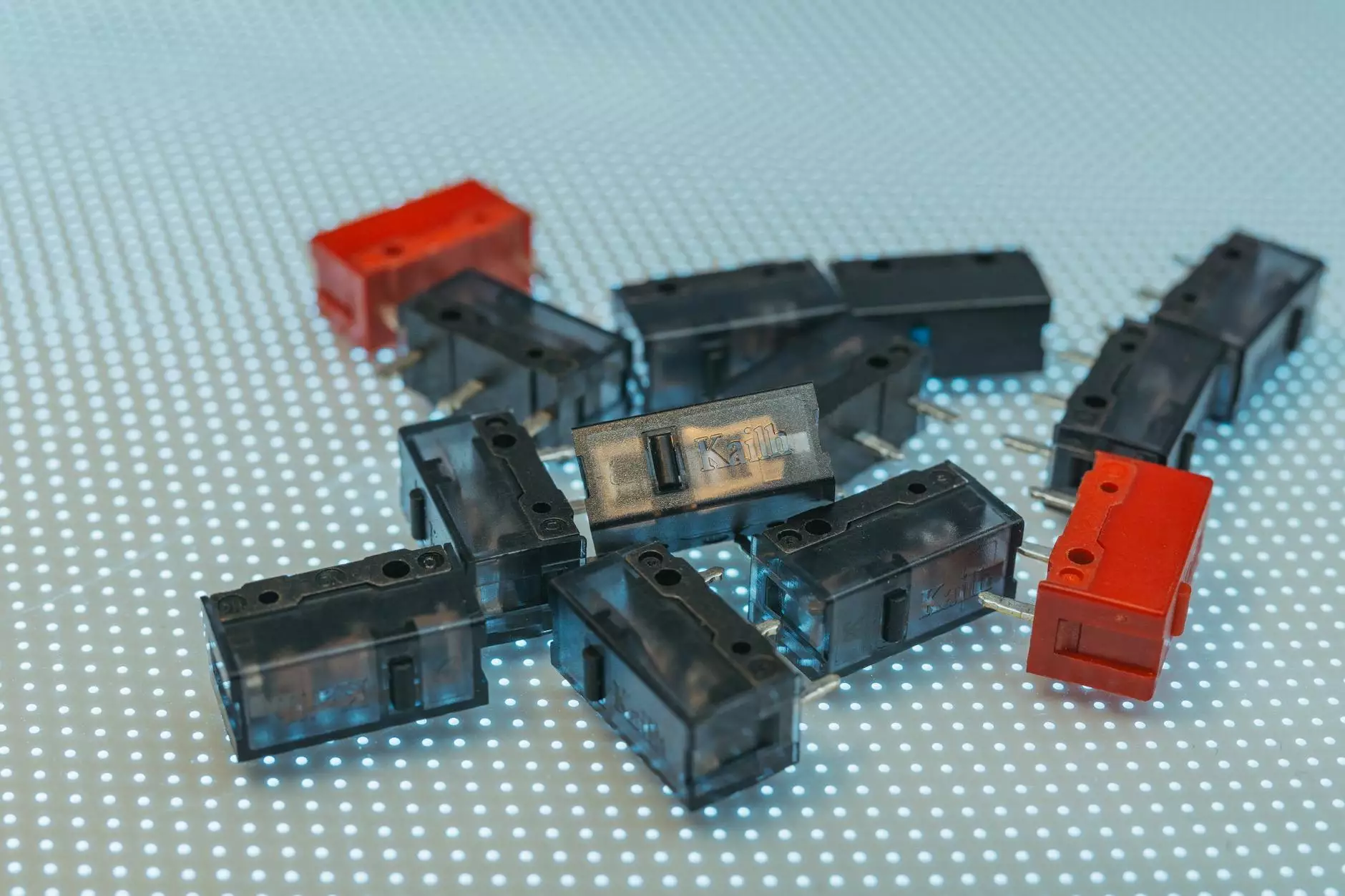
The realm of China mold manufacturing is vast and intricate, enveloping various disciplines and specialties that collectively shape the modern manufacturing landscape. More specifically, the focus on plastic mold making and plastic injection mould manufacturing has emerged as a cornerstone of production across diverse industries. This article serves as an in-depth exploration of these concepts, highlighting their significance, processes, and the exceptional expertise offered by companies like Hanking Mould.
The Evolution of Mold Manufacturing in China
Over the past few decades, China has transformed into a powerhouse in the mold manufacturing industry. This evolution can be attributed to several key factors:
- Technological Advancements: Modern machinery and software have revolutionized how molds are designed and fabricated.
- Skilled Workforce: A large pool of skilled professionals contributes to the efficiency and quality of mold manufacturing.
- Cost-Effectiveness: Competitive pricing in China attracts companies worldwide looking for reliable mold solutions.
- Global Partnerships: Many Chinese mold manufacturers have established strong relationships with international clients, fostering trust and collaboration.
What is a Mold in Manufacturing?
A mold is a hollowed-out block used to create a specific shape by pouring or injecting a liquid substance into it. The process usually involves:
- Designing the Mold: Initial sketches and CAD models are created to visualize the final product.
- Fabrication: The mold is fabricated using various materials such as steel or aluminum, depending on the application.
- Finishing: Surface treatments are applied to ensure the mold meets quality standards and precise specifications.
Types of Molds
In the context of plastic mold makers and plastic injection mould manufacturers, several types of molds are primarily used:
1. Injection Molds
This is the most common type of mold used in plastic manufacturing. The process involves:
- Melted plastic being injected into a mold cavity under high pressure.
- Cooling the plastic to solidify and form the desired shape.
2. Blow Molds
Blow molding is used to create hollow plastic parts. It involves:
- Heating plastic until it is malleable, then inflating it inside a mold.
- Commonly used for bottles and containers.
3. Compression Molds
Used mostly for thermosetting plastics, compression molding includes:
- Placing plastic resin into a heated mold cavity.
- Applying heat and pressure to mold the material into shape.
4. Rotational Molds
This method is ideal for creating large hollow products and consists of:
- A mold being filled with a powdered plastic material that is heated and rotated.
- Allows for even thickness and no weld lines in the final product.
Why Choose China for Your Mold Manufacturing Needs?
Opting for a China mold manufacturer, such as Hanking Mould, provides several benefits:
1. High-Quality Standards
Chinese manufacturers are increasingly adopting international quality standards, ensuring that the molds produced are durable and meet client specifications.
2. Quick Turnaround Times
With advanced machinery and skilled labor, Chinese manufacturers can often deliver high-quality molds faster than counterparts in other countries.
3. Innovation and Customization
Leading manufacturers in China are committed to continuous improvement and innovation, providing tailored solutions that meet unique customer requirements.
Understanding Plastic Injection Molding Process
The plastic injection molding process encompasses several stages:
1. Material Preparation
Granules of plastic are dried and prepared for melting before the injection process.
2. Injection
The prepared plastic is heated until it is molten and then injected into the mold at high pressure.
3. Cooling
After injection, the material cools and solidifies to form the final product shape.
4. Mold Opening and Ejection
Once cooled, the mold is opened, and the finished products are ejected, ready for further processing or assembly.
Key Considerations When Choosing a Plastic Mold Manufacturer
Selecting the right manufacturer is crucial for success. Consider the following factors:
1. Experience and Expertise
Look for manufacturers with a proven track record in the industry, ensuring they possess the necessary skills and knowledge.
2. Technology and Equipment
The best manufacturers utilize advanced technology that enhances precision and efficiency in mold production.
3. Customer Service
Effective communication and support are vital. A reputable manufacturer should be willing to assist throughout the project lifecycle.
4. Cost vs. Value
While competitive pricing is essential, prioritizing quality and service can yield long-term savings and benefits.
Future Trends in Mold Manufacturing
The future of China mold manufacturing is poised for exciting changes driven by innovation and technology, such as:
1. Automation and Robotics
Increased automation is expected to enhance production speed and accuracy while reducing labor costs.
2. Sustainable Manufacturing Practices
With an emphasis on environmental responsibility, manufacturers are adopting sustainable practices and materials.
3. Enhanced Design Capabilities
The use of advanced software and 3D printing technologies is improving mold design and accelerating prototyping processes.
Conclusion
In summary, the world of China mold manufacturing, particularly in the niches of plastic mold making and plastic injection mould manufacturing, presents vast potential for growth and innovation. Companies like Hanking Mould are at the forefront of this industry, offering high-quality, customized solutions that meet the needs of various industries. By understanding the processes, benefits, and future trends within this sector, businesses can make informed decisions and leverage the advantages of working with leading manufacturers in China.