Understanding the Role of a Plastic Injection Mold Maker
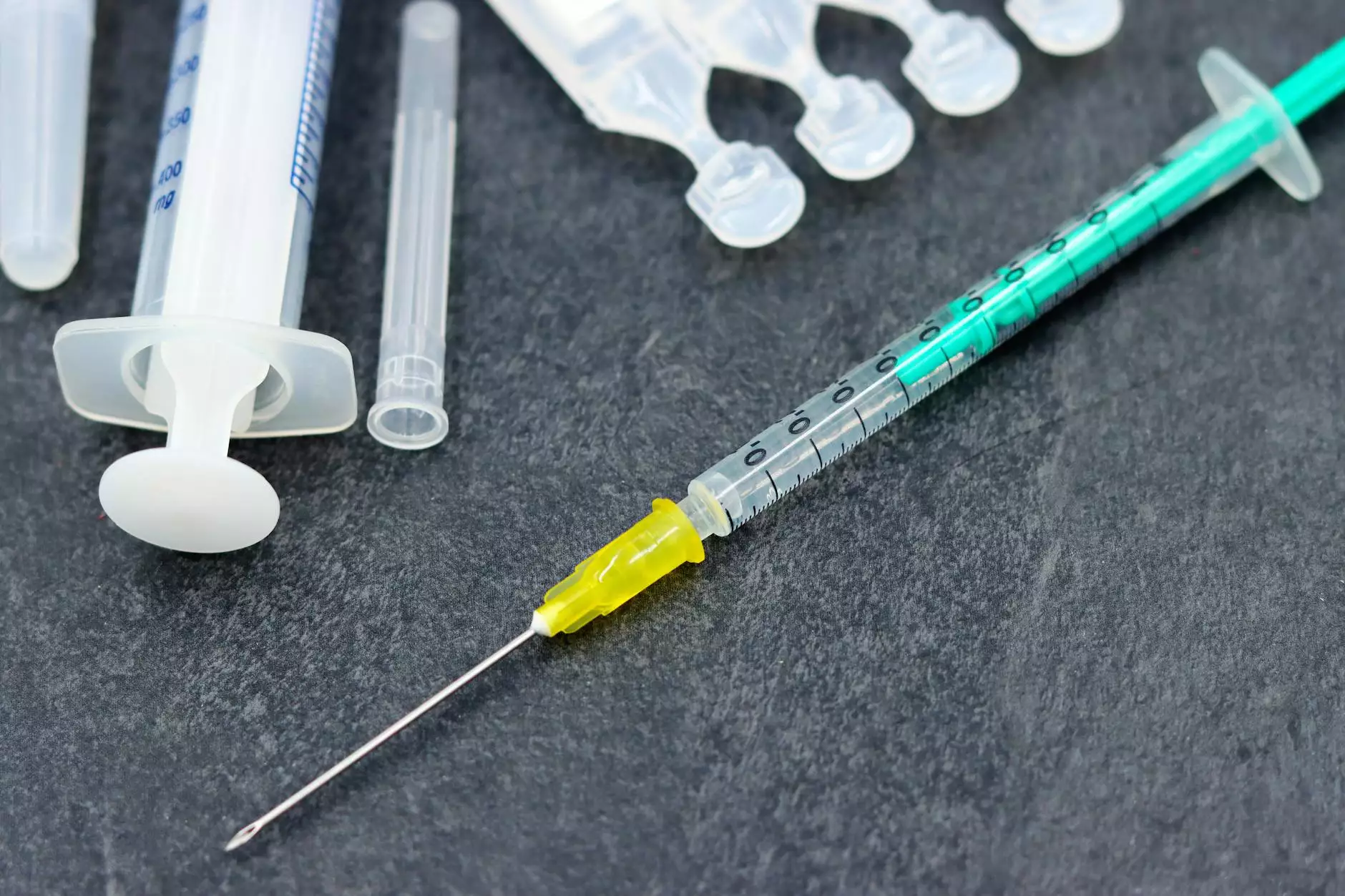
Plastic injection mold making is a crucial facet of modern manufacturing that significantly impacts various industries, from automotive to consumer goods. The need for precise and efficient production techniques has led to the rise of skilled plastic injection mold makers who play an essential role in developing high-quality molds for plastic products. In this article, we will delve into various aspects of plastic injection mold making, shedding light on its processes, benefits, and how companies like Hanking Mould excel in this field.
What is Plastic Injection Molding?
Plastic injection molding is a manufacturing process that involves injecting molten plastic into a pre-designed mold. This method is widely favored for its ability to produce parts with excellent detail, durability, and repeatability. Let's break down the key stages of this process:
- Designing the Mold: The first step in plastic injection molding is to design the mold. This involves precise engineering to ensure the mold will produce parts that fit exact specifications.
- Creating the Mold: Once the design is finalized, a mold is manufactured from durable materials like steel or aluminum, ensuring longevity and resistance to wear.
- Injection of Plastic: Molten plastic is injected into the mold under high pressure, allowing it to fill every cavity and detail of the mold.
- Cooling and Solidifying: The injected material is allowed to cool, after which it solidifies into the desired shape.
- Demolding: Finally, the mold opens, and the finished product is ejected. Quality control is then performed to ensure the part meets industry standards.
The Importance of Skilled Plastic Injection Mold Makers
The role of a plastic injection mold maker extends beyond just creating molds. Their expertise is pivotal in numerous areas:
1. Precision Engineering
A proficient mold maker employs advanced engineering techniques to ensure that every mold they create is precisely tailored to meet the specific requirements of the product. This precision is vital to guarantee that each produced part fits seamlessly into its intended application.
2. Material Selection
Choosing the right materials for both the mold and the injected plastic is critical. Plastic injection mold makers analyze numerous factors, including durability, cost-effectiveness, and the physical properties of the materials. For instance, using high-quality aluminum for molds can balance durability with cost efficiency, ideal for producing a large number of parts.
3. Problem Solving
Every project comes with its unique challenges. Experienced plastic injection mold makers are adept at troubleshooting issues and optimizing designs to enhance manufacturability. Their expertise can save manufacturers time and resources, boosting overall productivity.
Advantages of Plastic Injection Molding
The benefits of choosing plastic injection molding, particularly from a skilled plastic injection mold maker, are numerous:
- High Efficiency: Once the mold is created, mass production can begin swiftly, resulting in reduced lead times and high output.
- Consistency: Injection molding ensures that each part produced is consistently identical, which is essential in industries requiring high precision.
- Complex Shapes: The process allows for the creation of intricate and complex designs that might be unattainable through other manufacturing methods.
- Material Variety: A vast selection of polymers can be used, enabling manufacturers to achieve desired attributes such as flexibility, strength, or resistance to chemicals.
- Reduced Waste: The injection molding process generates minimal waste compared to subtractive processes, making it a more sustainable choice.
Applications of Plastic Injection Molding
Plastic injection molding finds applications in a wide range of industries, demonstrating its versatility:
1. Automotive Industry
From dashboard components to entire body panels, the automotive sector relies heavily on plastic injection mold makers to produce lightweight, cost-effective parts that enhance vehicle performance and reduce emissions.
2. Consumer Goods
Household items, toys, and appliances benefit from the precision and detail that injection molding offers, allowing for attractive designs that are both functional and durable.
3. Medical Devices
In the medical field, custom-designed components are created using injection molding under strict quality regulations, ensuring reliability and safety in sensitive applications.
4. Electronics
From casings and connectors to internal components, plastic injection molds are used extensively in the electronic industry to manufacture parts that require precise fit and finish.
How Hanking Mould Stands Out as a Plastic Injection Mould Manufacturer
Hanking Mould is renowned for its commitment to quality, innovation, and customer satisfaction. Here are several reasons why Hanking Mould is a preferred partner for businesses seeking reliable injection mold solutions:
1. Advanced Technologies
Utilizing the latest advancements in technology, Hanking Mould incorporates state-of-the-art machinery and software to enhance mold design and production processes. This commitment to innovation results in quicker turnarounds and higher quality products.
2. Skilled Workforce
The team at Hanking Mould consists of highly skilled professionals with extensive training and experience in mold making and production processes. Their expertise ensures unparalleled guidance and support throughout every phase of the project.
3. Custom Solutions
Every industry has specific needs, and Hanking Mould excels at providing tailored solutions that meet the precise requirements of its clients. Whether it’s a unique product design or specialized material requirements, Hanking Mould can accommodate various requests.
4. Quality Control
Quality is paramount, and Hanking Mould employs rigorous quality control measures throughout the manufacturing process. This dedication to excellence assures clients of reliable and high-performance molds that meet all industry standards.
5. Sustainability Practices
Recognizing the importance of environmental responsibility, Hanking Mould implements sustainable practices in its operations. This not only benefits the planet but also aligns with the growing demand for eco-friendly products in the market.
Conclusion
In sum, the role of a plastic injection mold maker is integral to the manufacturing landscape, providing essential services that drive innovation and efficiency in producing high-quality plastic parts. With companies like Hanking Mould leading the charge in the plastic injection mould manufacturing sector, businesses can rest assured that they have access to cutting-edge technology, expert craftsmanship, and unparalleled customer service. As the industry continues to evolve, the importance of skilled plastic injection mold makers will only grow, encouraging further advancements and possibilities in plastic production.